Oxford Thermofluids Institute | Research - Research Groups: CFD Group, Turbomachinery Aeroelasticity/Aeromechanics
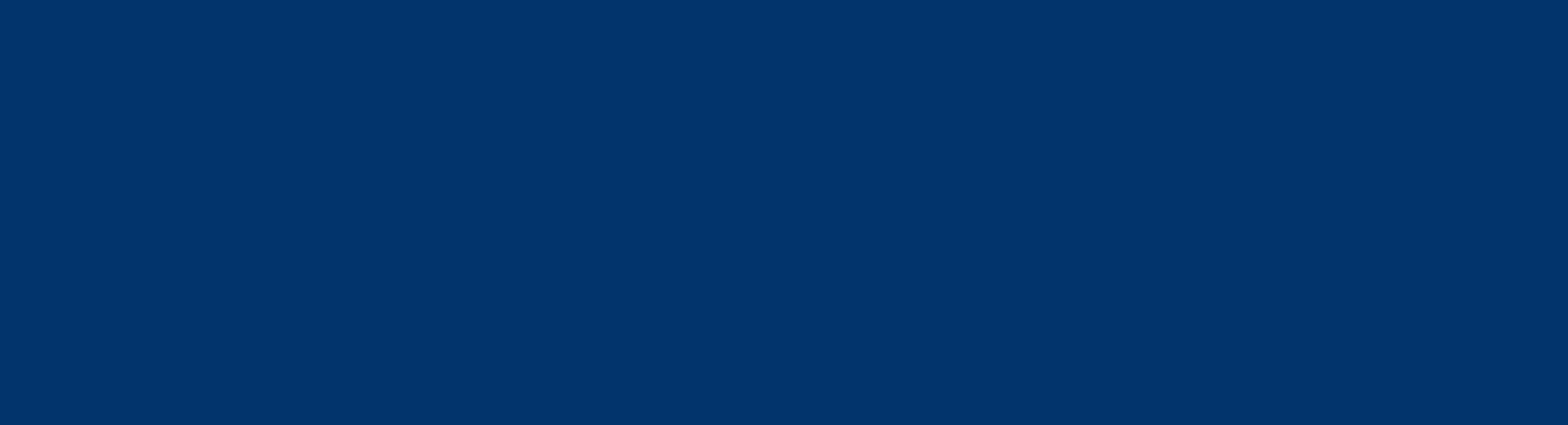
Turbomachinery Aeroelasticity/Aeromechanics
Blade flutter and forced-response prediction
Blade Flutter and Forced-Response Prediction Method Development
The direct coupled solution method is suited for prediction of aeroelastic behaviour of blade at highly loaded flow conditions with large scale self-excited flow instabilities (e.g. rotating stall). The simultaneous strongly coupled solution for both the blade structural dynamics equations and the Navier-Stokes floe equations was obtained using a multi-stage Runge-Kutta integration (He, 1994, 1996). The results for a compressor blade row at a transonic flow condition with and without the structure coupling show a rotating flow instability of a limit cycle type can be locked to the blade torsional structural mode with a relatively large frequency shift, leading to stall flutter.
For many turbomachinery applications, efficient and accurate predictions can be obtained by using a loosely coupled or decoupled approach, assuming the structural mode shapes and frequencies are not affected by aerodynamics. A prediction system for blade forced response and flutter has been developed (Moffatt et al, 2005) and its validity and effectiveness has been analyzed (Moffatt and He, 2005).
Oscillating blade experiments
Experimental Work
Somewhat out of a normally labeled pattern, for many years Li He has been carrying out and directing purpose built experimental studies from rig design, setting up, instrumentation, testing to data analysis. This line of research effort has been developed to a large extent due to the influence of his Ph.D supervisor and life-long mentor John Denton FRS, FREng, who has made an unparallel impact on modern turbomachinery CFD methods development and designs, while never believed in computer! This profound influence has been as strong after He was appointed a Chair in CFD at Oxford as when he was doing a Ph.D on Turbomachinery CFD at Cambridge many years ago.
Oscillating Aerofoil under Dynamic Stall (He and Denton, 1991)
We designed instrumented and tested an Oscillating Aerofoil over an incidence range from fully attached boundary layers to dynamic stall and fully stalled conditions. The combined ensemble averaged unsteady pressure data and the hot film raw traces give a unique insight into a large scale unsteady transition movement (inherently nonlinear) and its impact on modelling implication on aero-elastic prediction. The concept proof and evaluation of the quality of the off-board pressure transfers and the tubing attenuation formed a basis of further follow-on work.
Flow Visualization and Surface Pressures (Mean Incidence: 10 deg)
Surface Pressures and shear Stress (hot film) (Mean Incidence: 2 deg)
Oscillating LP Turbine cascade with Large Scale Separation (He, 1998)
There was (still is) a long ongoing debate in unsteady aerodynamics regarding the validity of the widely used time-linearised methods. The usual suspects of a breakdown of the linearised model are those with strong shock waves and flow separation.
A linear cascade of LP turbine blading was designed, setup and tested in the Whittle Lab duplex tunnel. A important feature of this blading relevant to the above general modelling issue is a large scale separation on the pressure surface from L.E. to 60% chord. There was also a small scale separation bubble on the suction surface. Unsteady surface pressure data give a detailed phase information re the reattachment of the suction surface bubble which evidently supported an adoption of a quasi-steady bubble length-transition model in He’s computational study. The unsteady pressures also indicated notable destabilising effect of the pressure surface long bubble.
In addressing the modelling issue, the results at different oscillation amplitudes showed a predominantly linear behaviour even with such a large scale flow separation. Interestingly, some recently presented experiment data showed a similar linear behaviour at a high speed (transonic) condition for a turbine cascade with separation and shock.
Oscillating Compressor and Turbine Cascades
Following the success of the 3D single blade oscillation test, a new rig was designed and commissioned. Two linear cascades, one for compressor blading and the other for turbine blades were designed, built and tested (all in a 3D oscillation flapping mode) as a part of two combined CFD and experimental projects. Although the primary purposes of the work were to provide quality data for code validation, the detailed 3D results (with different tip clearance gaps) also offer valuable insight into relevantly important flow physics for modelling development. These first-of-the-kind 3D results have now been published and the geometry, flow and oscillation conditions can be used for validations of 3D unsteady CFD codes for blade aeromechanics applications (contact Professor L. He, Li.He@eng.ox.ac.uk, if interested).