Oxford Thermofluids Institute | Facilities - Hypersonic Facilities
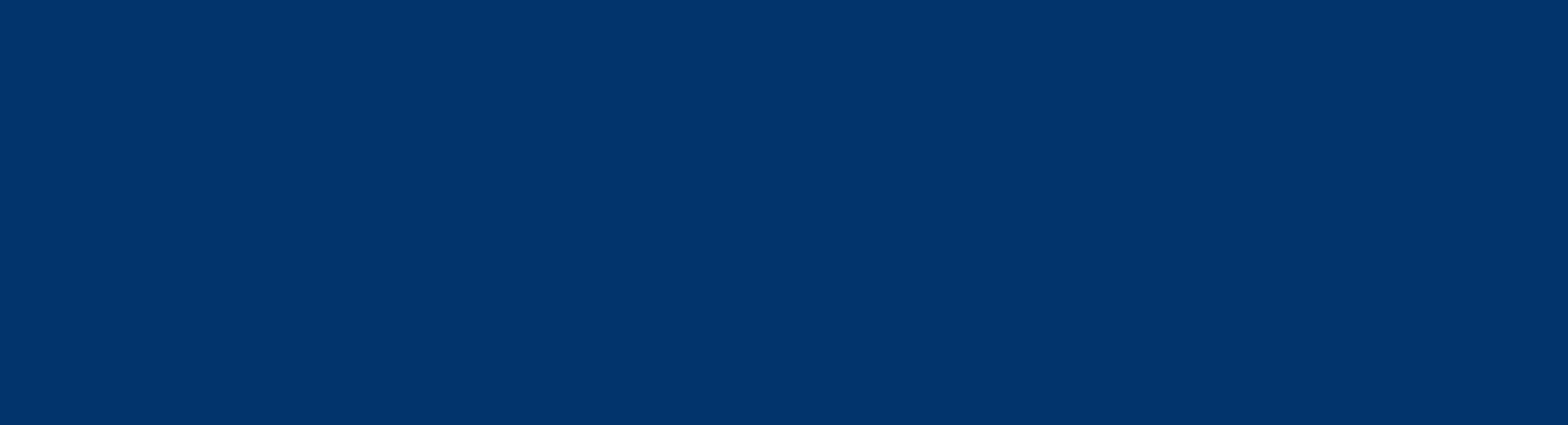
Hypersonic Facilities
The group has three world-class, high-speed wind tunnels, capable of producing flow from supersonic to hypersonic and all the way to hypervelocity:
Facility |
Mode |
Mach |
P0 [MPa] |
T0 [K] |
Test time [ms] |
T6 Stalker Tunnel |
Multi-mode Facility |
6-30 |
75/1000’s |
5000/10,000’s |
0.05-2 |
High Density Tunnel |
Ludwieg / LICH |
3-10 |
25 |
1250 |
70-500 |
Low Density Tunnel |
Suck down |
6-10 |
0.01 |
273 |
continuous |
The facilities are part of the National Wind Tunnel Facility. This offers a minimum of 25% access of the tunnels and instrumentation to outside parties (academic or commercial).
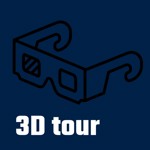
Hypersonics Facility
A 360 view of our Hypersonic T6 and HDT tunnels.
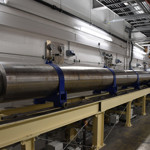
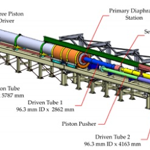


T6 Stalker Tunnel
The T6 Stalker Tunnel (T6) is Europe’s highest speed wind tunnel, capable of producing flows in excess of 20 km/s. It is a multi-mode facility, capable of operation either as reflected shock tunnel, an expansion tunnel or a shock tube. The facility is driven by the T3 free piston driver, designed by the late Prof. Ray Stalker, being one of the most powerful created in the world. The facility was developed by the University of Oxford (McGilvray and Doherty) in collaboration with the University of Queensland (Morgan and Gildfind).
T6 Stalker Tunnel specifications in different modes of operation:
Facility |
Reflected Shock Tunnel |
Expansion Tunnel |
Shock Tube |
Testing type |
Subscale model |
Subscale model |
Shock layer radiation |
Test duration |
1-3 ms |
50-500 μs |
2-50 μs |
Flow core diameter |
150-200 mm |
50-120 mm |
80 or 250 mm |
Max flow speed |
6.5 km/s |
12 km/s |
18 or 9 km/s |
Specifications:
- Free piston driver
- 9.5 m long, 300 mm dia. driver
- 250 MPa max pressure (cap at 75 MPa)
- Driven 1 & Driven 2 tubes
- 8.65 m long, 96.3 mm dia. shock tube
- Connections at 2.75 m, 7 m from P.D.
- Max 100 MPa (cap at 75 MPa, nominally Copper electroplated at throat
- Mach 7 and 8 contoured nozzles for reflected shock tunnel mode
- Aluminium Shock Tube
- 7 m long, 250 mm dia. shock tube
- Couples via expansion nozzle to Driven 1 tube
- Actuated traverse +/- 15 deg AoA. +/- 5 deg AoY
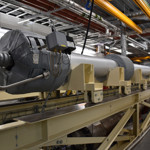
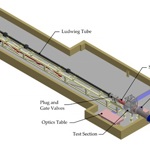


High Density Tunnel
The High Density Tunnel (HDT) is a reconfigured and upgraded facility from the original RAE shock tube, acquired by the University of Oxford in 2012. It operates either as a Ludwieg tunnel or a Light Piston Compression Heating facility, producing cold hypersonic flow conditions with test times long enough to investigate unsteady flow effects.
Specifications:
- Cold hypersonic flow facility for steady and unsteady aerothermodynamic testing
- Test durations up to 70 ms
- 6.5 m long, 152 mm diameter driver
- 17.4 m long, 152 mm diameter barrel
- Mach 3, 4, 5, 6, and 7 contoured nozzles
- Actuated traverse +/- 15 deg AoA. +/- 5 deg AoY
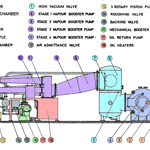
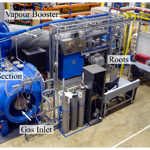


Low Density Tunnel
The Oxford Low Density Tunnel (LDT) is a hypersonic rarefied flow facility that has been in operation at the University of Oxford’s Department of Engineering Science since 1963. This wind tunnel operates as a free-jet, open-circuit, continuous-flow facility that produces hypersonic test flows primarily in the slip and transition regimes.
The test gas may be any inert gas and total temperatures up to ~550 K are currently possible, though there are plans to extend this to >1000 K. Acceleration of the test gas from the stagnation chamber is by way of a contoured Mach 6 nozzle, although conical nozzles and orifice plates have been used in the past to achieve free-molecular flow conditions [1, 2]. The current Mach 6 nozzle has an exit diameter of 108 mm and produces a core flow region of 40 mm diameter, depending on the test condition. Other Mach number nozzles may be developed in the range 4 to 12.
The test section consists of a large cylindrical vessel approximately 1540mm in diameter and 1500mm length with the axis perpendicular to the nozzle axis. Access to the test section may be from either side through full-size dished doors allowing for the installation of experimental kit.
The pumping system at the core of the facility is one of approximately four identical systems produced by Edwards Vacuum at the time of manufacture (early 1960s). It consists of an Edwards 100B4 ejector vapour booster pump backed by an 1R80 Roots-style mechanical booster pump and three HISC3000 rotary piston pumps. As a whole, the system is capable of pumping 22 000 l/s at back pressures up to ~2 Pa. With no gas admittance, the system is capable of achieving an ultimate pressure of ~0.01 Pa. The facility has been refurbished and recommissioned over the period 2014 – 2018, further details of which may be found in Donaldson et al. [3].
The Oxford Low Density Tunnel is suitable for experimentally investigating aero-thermal phenomena at high altitudes (approx. 70 – 90 km) such as control jets, multi-body interactions including shock-shock and shock-boundary layer interactions. It is well suited for characterising the heat transfer to satellites or debris during re-entry.
Experimental techniques currently employed include heat transfer measurements using liquid crystals, infrared thermography or thin-film heat transfer gauges and aerodynamic force measurements using a load-cell. A multi-axis traverse system is employed and an existing 3-component magnectic suspension balance system is to be recommissioned to enable precise force measurement and sting-free model attitude control.
Previously the LDT has been used to investigate:
- the heat transfer distribution on satellite anologue geometries (flat faced cylinders, hemisphere cylinders, etc)
- the effect of wall-to-temperature ratio on the drag of spheres and cones across the range of contimuum to free-molecular flow
- the variation in lift and drag of cones at angle-of-attack with Knudsen number
- wake flows behind vehicle analogue geometries
- comparisons between DSMC simulations and experimental drag measurements for cones and Aerobrake geometries
References
[1] Haslam-Jones, T. F., “Measurements of the Drag of Slender Cones in Hypersonic Flow at Low Reynolds Numbers using a Magnetic Suspension and Balance,” DPhil thesis, University of Oxford, Department of Engineering Science, Oxford, UK, 1977. Also Dept. of Eng. Sci. Report 1235/78 (1978).
[2] Hadjimichalis, M., “A Study of Sphere Drag in the Transition from Continuum to Free Molecular Flow,” DPhil thesis, University of Oxford, Department of Engineering Science, Oxford, UK, Oct. 1973. Also Dept. of Eng. Sci. Report 1073/73 (1973).
[3] Donaldson, N., Doherty, L. J., Ivison, W., Wilson, C. F., McGilvray, M., and Ireland, P. T., “Refurbishment and Characterisation of the Oxford Low Density Hypersonic Wind Tunnel,” International Conference on Flight Vehicles Aerothermodynamics and Re-entry Mission & Engineering (FAR), ESA, Manopoli, Italy, 2019.
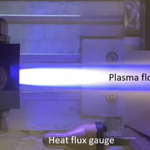
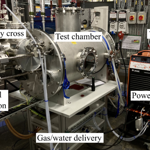

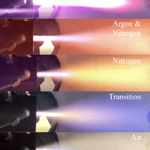




Osney Plasma Generator (OPG) plasma facility
OPG is a miniaturised plasma wind tunnel based on a thermal arc-jet plasma generator. The facility can provide continuous high-temperature plasma flows creating high heat fluxes representative of loads experienced during hypersonic flight. Two plasma generators are available (OPG1 and OPG2) which allow the testing of Argon, Nitrogen, and synthetic Air test gases. Material samples can be placed on a linear traverse system to position them in the plasma flow. The facility has been commissioned in 2023.
Specifications:
- Continuous high-enthalpy flows for material testing and plasma flow research
- Nozzle exit diameter 15mm or 30mm
- Arc-currents up to 500 A and powers up to 21.5 kW
- Test gases: Argon, Nitrogen, synthetic Air. Mass flows from 0.05 g/s to 10 g/s (with 0.2 g/s being typical)
- Vacuum (2000 Pa) to atmospheric pressure in test section
- Flow temperatures between 2,000K and 10,000K
- Flows ranging from subsonic conditions to Mach 3
- Lateral traverse for model and probe positioning
- Slug calorimeter and Pitot-probes for heat flux and pressure measurement
References
- Hermann, T., Chang, E. W. K. „Optical Temperature Measurement in Unsteady Plasma Free Jet“, Measurement Science and Technology 35(5) 055204 Jan 2024. DOI: 10.1088/1361-6501/ad24b7
- Valeinis, E. W. K. Chang, T. Hermann “Development and Testing of Slug Calorimeter and Total Pressure Probes for a Miniaturized Arc-jet” AIAA SCITECH 2024 Forum. American Institute of Aeronautics and Astronautics (AIAA). 08 Jan 2024. DOI: 10.2514/6.2024-2886
- Buquet, E. W. K. Chang, B. Williams, T. Hermann “Experimental Characterization of a Small Scale Arc-Jet Flow Using a Spatially Resolved UV-nIR Spectroscopy System” AIAA SCITECH 2024 Forum. American Institute of Aeronautics and Astronautics (AIAA). 12 Jan 2024. DOI: 10.2514/6.2024-2212
- Schaefer, E. W. K. Chang, T. Hermann, S. Loehle “Experimental Investigation of a Small-scale Arc-jet using Air Plasma” AIAA SCITECH 2024 Forum. American Institute of Aeronautics and Astronautics (AIAA). 12 Jan 2024. DOI: 10.2514/6.2024-2571
- W.K. Chang, T. Hermann "Commissioning Experiments for Small Scale Plasma Wind Tunnel OPG1", 34th International Symposium on Shock Waves (ISSW 2023), Daegu, Korea, 16 Jul 2023 - 21 Jul 2023. Springer.
- T. Hermann E.W.K. Chang, J. Schaefer, C. Joglekar, H. Boehrk "Development of Small Scale Arc-jet Facility OPG1", AIAA SCITECH 2023 Forum, National Habor, MA, USA, 23 Jan 2023 - 27 Jan 2023. DOI: doi/10.2514/6.2023-2334
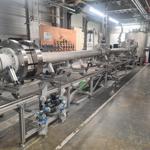

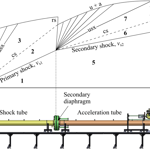



Cold-driven Expansion Tube CXT
CXT is a cold-driven expansion tube designed to produce flow velocities between 2 km/s and 6 km/s. The facility is approximately 12 m long and consists of a Helium driver (up to 80 bar), a shock tube , and acceleration tube of approximately 180 mm diameter. The facility utilises previous infrastructure of the T6 Stalker tunnel and the MCF Ludwieg Tube. A key feature is the operation of CXT in a hybrid mode which utilises the OPG plasma source to pre-heat models before exposure to a hypervelocity flow. The facility is currently in its commissioning phase.
Specifications:
- Cold Helium or air driver up to 80 bar
- Double-diaphragm operation
- 180 mm exit diameter
- Approximately 2-6 km/s flow velocities
- Test durations approximately 200 microseconds