Oxford Thermofluids Institute | Facilities - Engine Component Aerothermal Facility (ECAT)
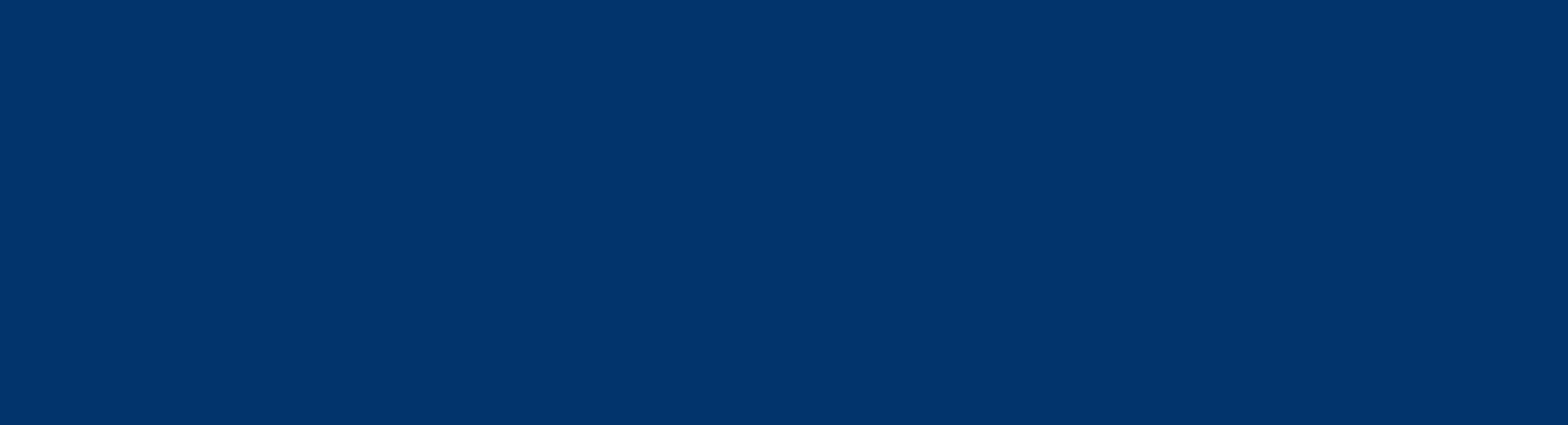
Engine Component Aerothermal Facility (ECAT)
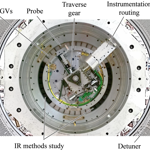
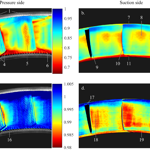


Engine Component Aerothermal Facility (ECAT)
The Engine Component AeroThermal (ECAT) facility has a modular working section which houses a full annulus of engine components. The facility is currently operated with high-pressure nozzle guide vanes from a large civil jet-engine. A high degree of engine similarity is achieved, with matched conditions of Mach number, Reynolds number, and coolant-to-mainstream pressure ratio. For combustor-turbine interaction studies, a combustor simulator module is used, which is capable of both rich-burn and lean-burn combined temperature, swirl and turbulence profiles. The facility is being used for aerothermal optimisation research (e.g., novel cooling systems, aerodynamic optimisation problems, capacity sensitivity studies), computational fluid dynamics validation (aerodynamic predictions, conjugate predictions), and for component validation to accelerate the engine design process.
The three key measurement capabilities are: capacity characteristic evaluation to a precision of 0.02%; overall cooling (metal) effectiveness measurements (using a rainbow set of parts if required); and aerodynamic loss evaluation (with realistic cooling, trailing-edge flow etc.). Each of these three capabilities have been separately developed and optimised in other facilities at the University of Oxford in the last 10 years, to refine aspects of facility design, instrumentation design, experimental technique, and theoretical aspects of scaling and reduction of experimental data. The ECAT facility brings together these three research strands with a modular test vehicle for rapid high technology-readiness-level research, demonstration of new technologies, and for engine component validation.
The ECAT facility is a response to the changing requirements of experimental turbomachinery testing, and it is hoped this paper will be of interest to engine designers, researchers, and those involved in major facility developments in both research institutes and engine companies.
The three key capabilities of the facility are as follows:
- Capacity measurements are possible with a precision error of 0.02%, allowing designers to assess the performance of HPNGVs at an early point in the engine design cycle and evaluate the impact of novel design features. Measurements are conducted with real engine parts blowing at engine representative conditions. Parametric studies are made possible by exceptionally low precision error of the facility, allowing fundamental research on a number of aerodynamic topics (trailing edge design and performance, cooling mixing loss, coolant migration, shock control etc.)
- Metal effectiveness measurements are possible with a very high level of precision allowing designers to test rainbow sets of HPNGVs at an early point in the engine design process, for precise back-to-back ranking of the overall thermal performance of designs. Biot number can be matched in these experiments allowing direct comparison with engine thermal paint test data. Thermal data can be used for assessment of conjugate CFD capability, used as a top-down way of extracting individual boundary conditions for optimisation research, or for high fidelity modelling of novel cooling schemes.
- Aerodynamic performance measurements are possible, allowing design ranking under highly engine realistic conditions of Mach, Reynolds, cooling flow, turbulence etc. This is significant because many historic optimisation studies have ignored real-engine effects, which can significantly modify absolute performance values and change performance ranking.
The development of ECAT is a response to the current requirement for rapid assessment of complex HPNGV designs, the maturation of DLD manufacturing technology (allowing preliminary aerothermal assessments ahead castings), and the developments in top-down academic research (decoupling of whole-system information) which have opened up fruitful areas for fundamental study.
For more information on the work that led to the development of the ECAT facility, a description the facility, and an analysis of the accuracy and utility of the techniques, please consult the following paper: Benjamin Kirollos, Roderick Lubbock, Paul Beard, Frédéric Goenaga, Anton Rawlinson, Erik Janke, Thomas Povey, 2017, “ECAT: An Engine Component Aerothermal Facility at the University of Oxford,” ASME Turbo Expo 2017, Paper No. GT2017-64736, pp. V02AT40A032; 14 pages doi:10.1115/GT2017-64736.