Nozzle Guide Vane Capacity Facility
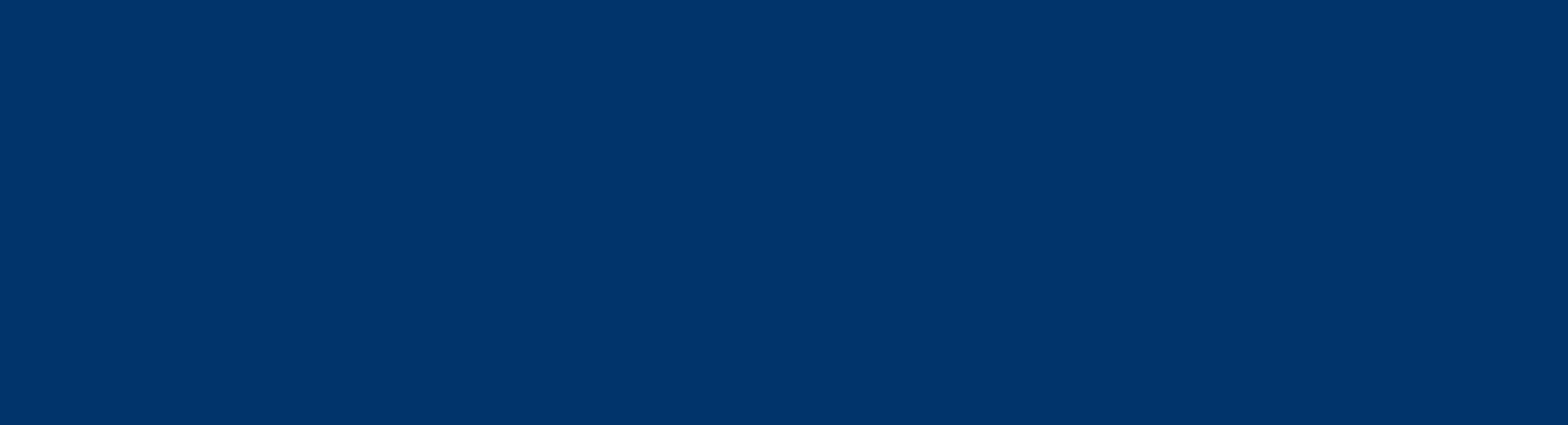
Nozzle Guide Vane Capacity Facility
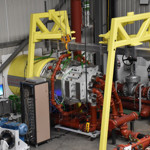
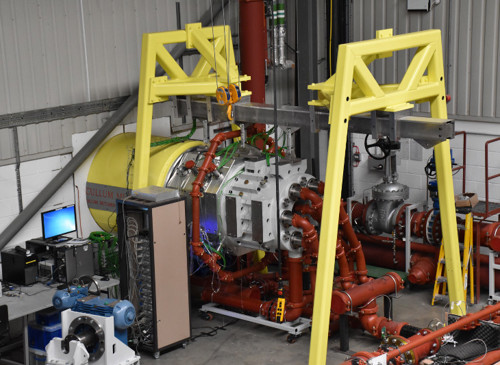
Nozzle Guide Vane Capacity Facility
This is an engine-parts facility at the University of Oxford for high technology-readiness-level research and for engine component validation.
The Nozzle Guide Vane (NGV) Capacity facility was developed at Oxford over 15 years using a novel semi-transient method for making experimental measurements of the capacity of engine-parts. It has been proven to offer equivalent measurement accuracy to continuous-running facilities, at greatly reduced cost.
The recently updated facility has a modular working section which houses a full annulus of engine components and allows for improved test programme efficiency. The facility is currently operated with high-pressure nozzle guide vanes from a large civil jet-engine, complete with coolant air supply. A high degree of engine similarity is achieved, with matched conditions of Mach number, Reynolds number, and coolant-to-mainstream pressure ratio.
Capacity measurements are possible with a precision error of 0.02%, allowing designers to assess the performance of HPNGVs at an early point in the engine design cycle and evaluate the impact of novel design features. Measurements are conducted with real engine parts blowing at engine representative conditions. Parametric studies are made possible by exceptionally low precision error of the facility, allowing fundamental research on a number of aerodynamic topics (trailing edge design and performance, cooling mixing loss, coolant migration, shock control etc.)
An actuated traverse gear installed downstream of the working section and the ability to accurately maintain the facility operating conditions at steady state for a period of up to 60 seconds provides the capability to conduct full-area surveys of the exit flow field, generating aerodynamic performance measurements under highly engine realistic conditions of Mach and Reynolds numbers and realistic film cooling and trailing edge flows.
For more information on the development of the transient technique and the Capacity facility, a description the original facility and its operation, and an analysis of the uncertainty in the measurements, please consult the following paper:
[1] Povey, T., Sharpe, M., Rawlinson, A., 2011, “Experimental Measurements of Gas Turbine Flow Capacity Using a Novel Transient Technique”, ASME J. Turbomach., 133(1), 15 pages doi:10.1115/1.4000481.
The facility has been used for computational fluid dynamics (CFD) validation, component validation to accelerate the engine design process, and for aerodynamic optimisation research – including studies of the sensitivity of the capacity and aerodynamic flow field measurements to vane surface film cooling configuration and trailing edge coolant ejection geometry. The group also performs theoretical and numerical work which compliments the experimental facility.
[2] Povey, T., 2010, “Effect of Film Cooling on Turbine Capacity”, J. Eng. Gas Turbines Power, January 2010, 132(1), 10 pages doi:10.1115/1.3026564
[3] Hambidge, C., Povey, T., 2012, “Numerical and Analytical Study of the Effect of Film Cooling on HP NGV Capacity”, ASME Turbo Expo 2012, Paper No. GT2012-69066, pp. 1347-1358; 12 pages doi:10.1115/GT2012-69066.